Calibrating vegetable spreaders and sprayers
Spring time is the best opportunity to lock in your output rate with a range of machines, settings and products.
Herbicides, insecticides, and in some cases fungicides, are all being sprayed for the first time this season. In addition, granular fertilizers are being spread too. While many of the machines that are used for these applications have manuals and tables to reference, nothing beats an actual measurement of output. It’s a good idea to do this before the maiden voyage of the season, if for no other reason than to get your first equipment breakdown out of the way before applying for real! One of the greatest mysteries on earth is how a sprayer can go into winter storage clean as a whistle and then come out with clogged filters and stuck pumps.
In my capacity as a vegetable person, I have been calibrating boom and backpack sprayers the same way for years using the 1/128th of an acre method. I’m sure you’ve seen it somewhere, perhaps on a sticker affixed to a spray tank. It skips some math with a clever trick. When spraying 1/128th of an acre (340 square feet), the number of fluid ounces collected is equivalent to the rate applied in gallons per acre, because there are 128 fluid ounces in a gallon.
How it works
Picture a rectangle that has an area of 340 square feet (1/128th of an acre). The length of the short side is defined by your nozzle coverage, while the long side is the distance you need to travel to cover 340 square feet. For boom sprayers, I measure the average distance between nozzles and try to adjust them so they are all the same spacing. My herbicide sprayer has 24-inch spacings. That 24 inches (or 2 feet) is the short edge of a skinny rectangle that is 1/128th of an acre, or 340 square feet. So, 340 feet / 2 feet = 170 feet for the long edge. You then mark that out, set your desired ground speed and pressure, and time yourself driving that distance. It took me 37 seconds in gear B1 with the RPMs at 2250. Then, you park the tractor, run the sprayer at the same RPMs and collect the spray from one of the nozzles for the same amount of time. In 37 seconds, I collected 18 fluid ounces of water.
Because of the nifty 1/128 ratio trick, that 18 fluid ounces actually represents 18 gallons per acre of output. I will do this for two or three nozzles and inspect the others for visual abnormalities in their pattern. From there you figure out your dilutions to ensure the right amount of active ingredient is added to the tank for your desired application rate.
The same basic procedure is used for banding or directed nozzle sprayers, but you use the width of the band, or the distance between directed nozzle groupings as your short edge, no matter how many nozzles. You could have three nozzles forming a box of spray from above and both sides of a trellised tomato row, for example. Measure the distance between the center of each grouping for the short side of your 1/128th acre rectangle, calculate the long side distance, travel it, time it and collect the output from all three nozzles for that same period of time.
How about a wand sprayer attached to a hand-pump tank or a backpack?
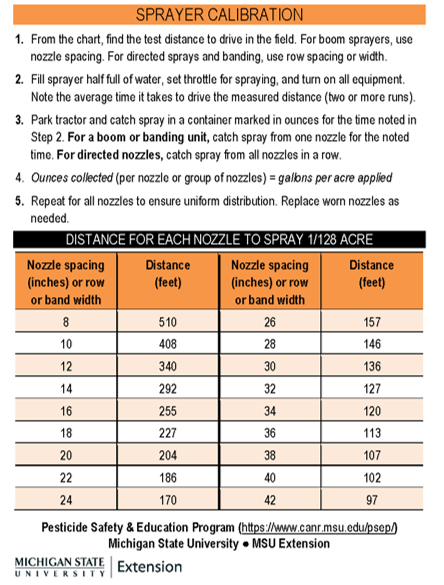
These are usually light enough and easy enough to fill, spray over any size of area, and remeasure what is left to find output. But, to save brain cells, I use the 1/128th method for this as well. I choose my target: a row of trellised tomatoes. The plants are 3 feet tall, and I spray one side of the row at a time with an up and down motion like with a paint roller on a wall. In this case, 3 feet is the short side of my rectangle, therefore the long side is 113 feet (340 square feet / 3 feet). I put in my earbuds, load up “Staying Alive” by the Bee Gees, and time myself walking the 113 feet while spraying up and down to the beat. The rest of the procedure follows exactly as the boom sprayer example above. Measure in fluid ounces for the same time it took to travel 113 feet and you have your output in gallons per acre.
The tricky part with hand-pump sprayers is the hand-pumping. Your pressure consistency can vary if you are not careful. Electric, CO2 and gas-powered backpack sprayers reduce that variation.
This is often the best you can do to ensure you get some semblance of proper coverage and delivery. However, you may learn that during an actual spray, the dynamics change. For example, the herbicide sprayer I calibrated above at 18 gallons per acre ended up delivering my application at only 15.4 gallons per acre. I determined this by filling the tank to a volume that was a little bit larger than what I calculated I needed to make the spray, then counted the number of passes it took me to empty it. After I sprayed my plots, I sprayed another area to drain the tank. My passes were 20 feet wide and 630 feet long (12,600 square feet, or 0.29 acre). I used all 85 gallons of solution in 19 passes. I calculated 15.4 gallons per acre from 85 gallons / (0.29 acre x 19 passes). Such is life.
Does this work for spreaders?
Since this method worked reasonably well for me over the years, I wanted to try it out with a fertilizer spreader. Like the 1/128th method, you need to make a rectangle that is in this case 1/16th of an acre (2,723 square feet). It works smoothly if you can measure dry weight in ounces. If you measure in pounds, you just need to multiply by 16. I guess we can call it the 1/16th method.
You have to imagine that the nozzle is the pendulum, spinner or drop holes, and that the short side of your rectangle is the “effective swath width.” A swath width for a drop spreader is simply the width of the drop chute. For all other flingers and spinners, this width changes depending on the height and angle of the spreader, and the density, shape and hardness of the product. So, your effective swath width is something that should be measured for each individual product or each blend you will be using.
As an example of how hardness factors in, there is an agitator at the bottom of a spreader cone to break up bridging and ensure proper flow through the gates. However, with a lot of weight pressing down on this point and a small gate opening, the agitator can become a pulverizer, smashing granules into a dust before they exit the gates. Dusts and splintered granules behave differently in their trajectories than a full-sized granule. Potassium chloride seems to be especially susceptible to this, and brittle or soft products like that benefit from a larger gate opening to keep granules moving, and a higher travel speed to maintain a proportional broadcast rate.
Some manufacturers provide guidance on the expected swath width for various products using particular gate settings. For my Vicon pendulum spreader, I measured effective swath width by putting 11 bus bins in a line, 5 feet apart. Then, I filled the spreader, locked in my RPMs at 2250 and gearing at B2, chose a gate setting based on the equipment manual (18, in this case), and drove over the middle bin with the spreader engaged about 10 times.
I shook all the granules down into one corner of the middle bin and started comparing the pile with the piles in every other bin. The bin that has 50% fewer granules marks the edge of the effective swath width. In my case, that bin was 10 feet away from the center bin. I checked the bins on the other side of the swath as well and found the same result. So, with 10 feet on either side, my effective swath width was 20 feet. That was the short side of my rectangle.
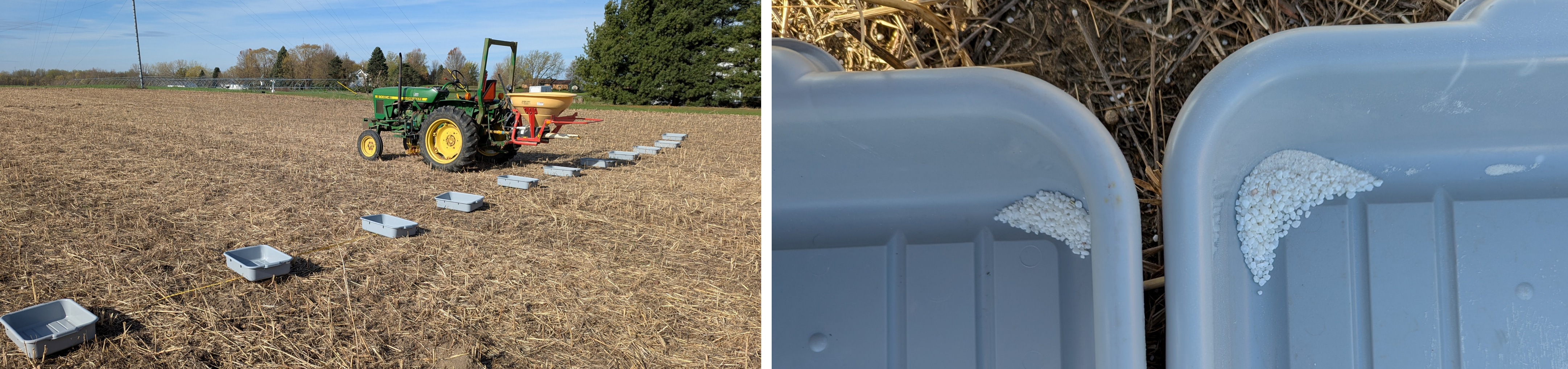
The long side of my rectangle was calculated as 136 feet (2,723 square feet / 20 feet). Similar to the sprayer example, I then marked out 136 feet and timed myself driving it at the same gear and RPM as I intended to use at application. It took me 21 seconds. With that information handy, I had to find a way to collect the ounces of output from my spreader. For ground-driven spreaders, you may need to jack up the spreader and rotate the tire the same number of rotations that it takes to drive the long-side of the rectangle and collect the granules from the end of the conveyor. For my Vicon, I removed the long pendulum flinger and set up a collection system with cardboard and fertilizer bags to funnel all the granules into a bin. Your solution may be more elegant.
With the tractor stationary, RPMs set, gate at 18 and PTO engaged, I opened the feed gate and started a stopwatch simultaneously. After 21 seconds, I shut the feed gate. Then I weighed the granules, and found that it delivered 208 ounces, which is equivalent to 208 pounds per acre because one dry ounce is 1/16th of a pound. If I had weighed the granules in pounds, I would have multiplied that number by 16 to convert to ounces (and the pound per acre equivalent).
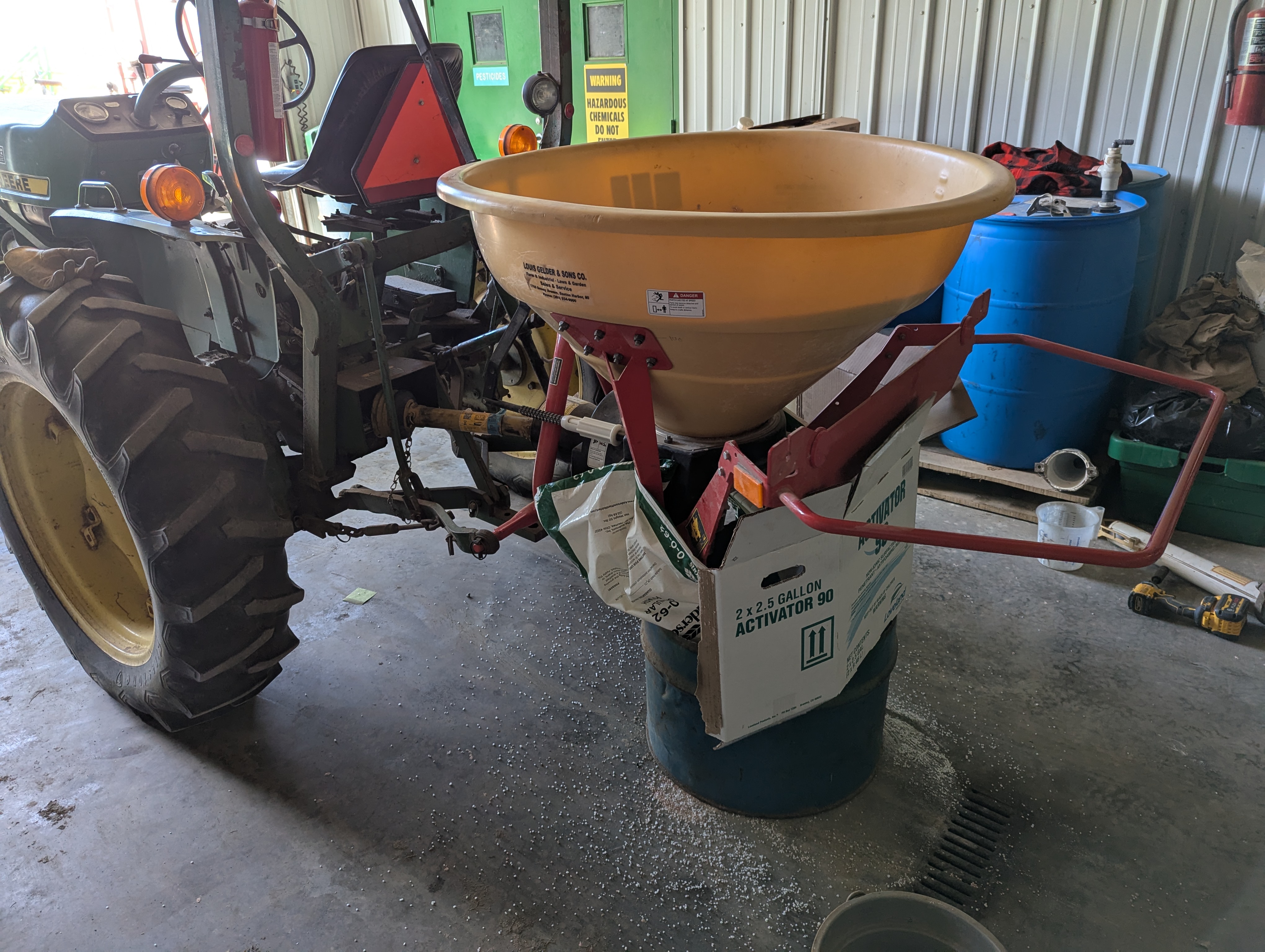
Great! But I wanted to apply this product at 100 pounds per acre. So, I set the feed gate to 9 and tried again. This time I measured 64 ounces. Too short! A gate setting of 12 got me to 92 ounces, which was good enough for me. However, like the sprayer, mysterious forces cause slightly different outputs, such as wheel slippage and driving without guidance technology. For example, even though I calibrated each ingredient separately to apply approximately 100 pounds per acre, my ammonium sulfate application delivered 93.75 pounds per acre, my ammonium nitrate was delivered at 115 pounds per acre, and my potassium chloride went down at 85.7 pounds per acre. With the rest of the season’s fertility going in through the drip, this is an acceptable variation and can be adjusted for later if need be. However, the knowledge you gain from actually calibrating and testing your equipment each year will help you dial in applications better next time.
For more information on sprayer and spreader calibration, including technical descriptions, tables, formulas and examples, check out these excellent resources: